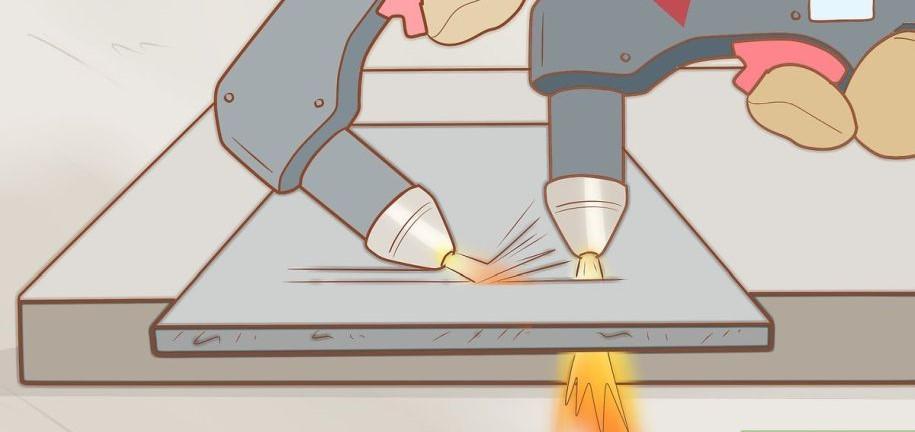
W skład stanowiska do cięcia plazmą wchodzi:
-
źródło prądu wraz z układem sterowania czyli przecinarka plazmowa,
-
wielofunkcyjny przewód z palnikiem plazmowym (uchwytem do cięcia plazmą) doprowadzający prąd do elektrody nietopliwej, gaz plazmowy, sterowanie oraz opcjonalnie układ chłodzenia,
-
przewód masowy z zaciskiem łączący cięty przedmiot ze źródłem prądu,
-
źródło gazu plazmowego i osłonowego - najczęściej sprężarka powietrza,
-
opcjonalnie - układ wodnego chłodzenia uchwytu - chłodnica cieczy.
Jak ciąć ręczną przecinarką plazmową - podstawowe informacje
Przed przystąpieniem do cięcia plazmowego należy podłączyć przecinarkę do zasilania elektrycznego oraz do źródła sprężonego powietrza (sprężarka, sieć sprężonego powietrza). Zgodnie z instrukcją producenta należy ustawić odpowiednie ciśnienie powietrza na manometrze. Przewód masowy należy zakleszczyć na ciętym materiale.
Przed rozpoczęciem cięcia należy odpowiednio dobrać wymienne elementy palnika (elektroda, dysza) i ustawić wartość natężenia prądu zgodnie z zaleceniami producenta biorąc pod uwagę grubość i rodzaj ciętego materiału.
Proces cięcia rozpoczyna się od naciśnięcia przycisku na uchwycie, czemu towarzyszy zapalenie się łuku pilotującego, który w zetknięciu z materiałem ciętym powoduje zajarzenie łuku głównego. Wyłączenie przycisku powoduje zakończenie procesu cięcia.
Proces cięcia jest manualnie łatwiejszy od spawania, gdyż sprowadza się do właściwego przesuwania palnika wzdłuż zadanej linii cięcia z odpowiednią prędkością. Odpowiednia wprawa operatora wymagana jest właśnie do uzyskania prawidłowej prędkości przesuwania palnika.
Podstawowe parametry procesu cięcia plazmą
-
Natężenie prądu - natężenie prądu decyduje o temperaturze i energii łuku plazmowego. Zwiększając natężenie prądu możemy zwiększyć prędkość cięcia lub grubość przecinanego materiału.
Zbyt duże natężenie prądu sprawia, że pogarsza się jakość cięcia, zwiększa szerokość szczeliny, pojawiają się zaokrąglenia górnych krawędzi i odchylenie od prostopadłości. Zbyt małe natężenie prądu powoduje natomiast początkowo pojawienie się nawisów metalu przy dolnej krawędzi, a następnie brak przecięcia.
Natężenie prądu jest parametrem bezpośrednio regulowanym w przecinarce. -
Napięcie łuku - Napięcie łuku plazmowego decyduje o sprawnym przebiegu procesów cięcia plazmowego i stąd musi być dokładnie sterowane. W zależności od natężenia prądu, napięcie łuku - ze względu na bardzo duży stopień koncentracji plazmy łuku - wynosi od 50 do 200 V.
-
Prędkość cięcia - prędkość cięcia należy odpowiednio dobrać do natężenia prądu i grubości ciętego materiału. W przypadku cięcia ręcznego duże znaczenie ma doświadczenie operatora. Podobnie jak wartość natężenia prądu, również prędkość ma wpływ na jakość przeprowadzonego cięcia. Zbyt mała prędkość prowadzi do zwiększenia szerokości szczeliny i pojawienia się nawisu metalu i żużla przy dolnej krawędzi oraz zaokrąglenia górnej krawędzi cięcia odchylenia od prostopadłości. Zbyt duża prędkość daje w efekcie zjawisko identyczne, jak w przypadku zbyt małego natężenia prądu.
-
Grubość cięcia - do grubości przecinanego materiału należy dopasować natężenie prądu i prędkość cięcia zgodnie z zaleceniami producenta. Im grubszy materiał tym większe natężenie prądu i mniejsza prędkość cięcia.
Producenci przecinarek podają maksymalną grubość cięcia danej przecinarki plazmowej dla poszczególnych materiałów określając ją w dwóch wartościach:
- maksymalna grubość cięcia jakościowego - czyli cięcia po którym powierzchnia materiału w miejscu rozcięcia jest dobrej jakości,
- maksymalna grubość cięcia rozdzielającego - czyli cięcia za pomocą którego rozdzielimy materiał, ale bez zachowania dobrej jakości krawędzi cięcia. -
Rodzaj i ciśnienie oraz natężenie przepływu gazu plazmowego - Prędkość wypływu strumienia plazmy z palnika, oraz jego temperatura, są zależne od natężenia prądu, średnicy i kształtu dyszy zwężającej, a także odległości palnika od ciętego przedmiotu. Wpływ ma również rodzaj gazu plazmowego i jego ciśnienia. To właśnie dlatego, w zależności od rodzaju ciętego materiału, stosowane są różne gazy plazmowe. W pierwszych urządzeniach do cięcia plazmowego stosowany był wyłącznie argon i mieszanki argonu z wodorem. Ze względu na wysoką cenę tych gazów, rozwój cięcia plazmowego zmierzał nie tylko w kierunku zwiększenia jakości i prędkości cięcia, lecz również zastąpienia argonu znacznie tańszymi gazami. Początkowo był to azot, a następnie powietrze i tlen. Obecnie w popularnych przecinarkach ręcznych stosuje się zasilanie sprężonym powietrzem. Wymagane ciśnienie powietrza jest podawane przez producentów przecinarek i waha się w granicach 4÷7bar.
-
Rodzaj i konstrukcja elektrody - producenci palników plazmowych stosują różne rozwiązania konstrukcyjne elektrod i ich zamocowania i chłodzenia dążąc do wydłużenia czasu ich pracy i polepszenia jakości cięcia. Średnicę elektrody należy dobrać w zależności od natężenia prądu i należy polegać na zaleceniach producenta. Należy pamiętać, że zwiększanie natężenia prądu powoduje zwiększone zużycie elektrod.
-
Średnica dyszy zwężającej - dobór dyszy należy przeprowadzić zgodnie z zaleceniami producenta.
-
Położenie palnika względem ciętego przedmiotu - palnik plazmowy jest prowadzony prostopadle do ciętej powierzchni i w zależności od konstrukcji palnika dysza może się bezpośrednio stykać z ciętym materiałem, co zwiększa jakość cięcia lub też zachowywać pewien odstęp dzięki zamocowanej sprężynie dystansowej.
Żłobienie plazmowe
Przecinarki plazmowe stosowane do cięcia mogą być wykorzystywane również do żłobienia. Proces żłobienia wykonuje się zazwyczaj za pomocą standardowych palników do cięcia, lecz wyposażonych w specjalne dysze i prowadniki utrzymujące palnik we właściwej pozycji. Podczas żłobienia palnik skierowany jest pod kątem ostrym w stosunku do obrabianej powierzchni, dzięki czemu stopiony materiał jest wydmuchiwany na zewnątrz bez przecinania materiału.